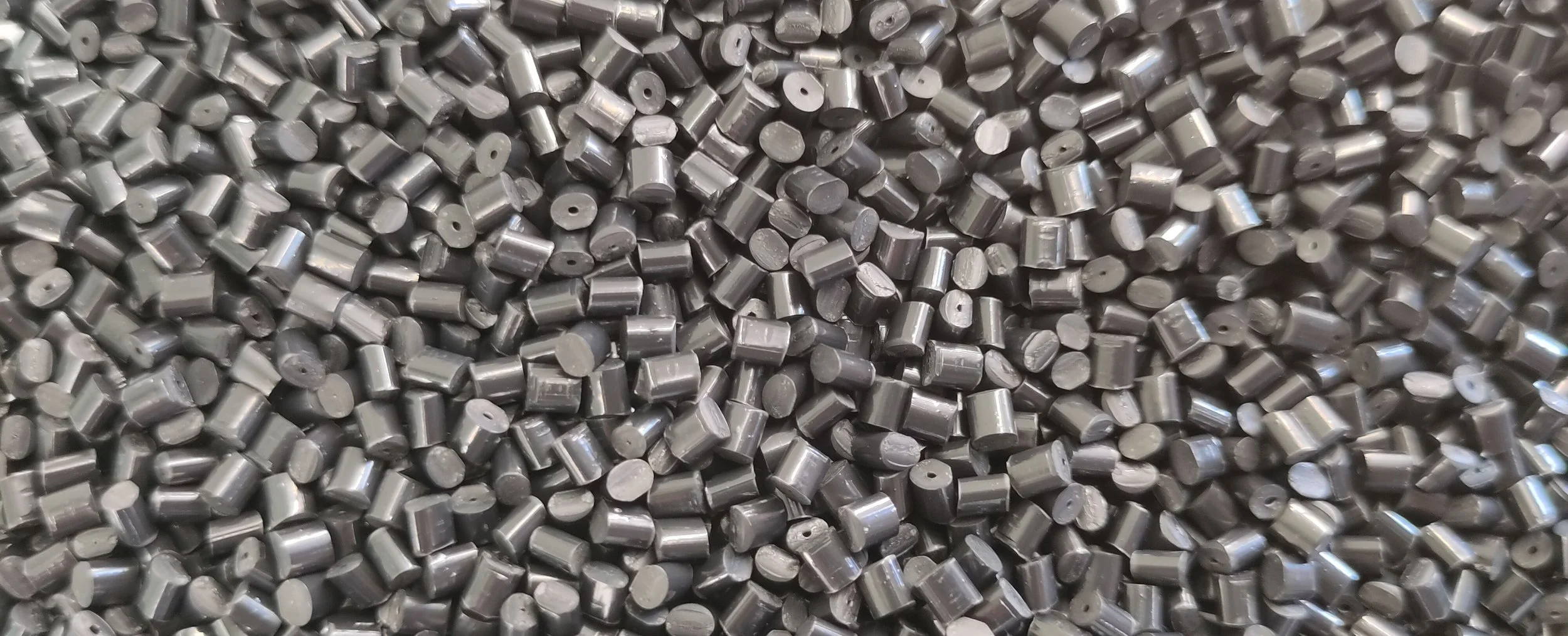
Ecodesign guidelines
Ecodesign to promote circularity of hazardous plastics
Ecodesign as a concept originates in the 1990’s from the area of product design and technical innovation. The emphasis is on considering the environmental impacts for the full lifecycle, from raw-material extraction through to product use and end-of-life. The ecodesign process demands making environmental considerations for both production and consumption.
The ecodesign opportunities and choices link to several actions along different stages of the plastics value chain. As a result, considerations and criteria to improve circularity of potentially hazardous plastics in the NONTOX context can be connected to specific opportunities and actors (see a more detailed table here).
Waste Electrical and Electronic Equipment (WEEE) comprises several types of products that often have a relatively short product lifespan and can in theory be efficiently collected and treated through recycling processes. There is also potential in extending the product life such as through repairability and through secondary markets.
Whilst the variety of products, components, and materials in the WEEE stream can be a challenge for recycling, there are plenty of opportunities. In end-of-life management, after crushing and sorting of the remaining waste stream, the mixed plastic fraction can be further sorted based on polymer type and presence of flame retardants and recycled by more advanced means, but it is still most commonly incinerated.
WEEE is mainly collected through community waste collection sites or taken back by retailers. In the EU, extended producer responsibility (EPR) is mandatory within the WEEE Directive, which puts the responsibility for the collection, recycling and end-of-life disposal of WEEE on the producers.
Ecodesign for WEEE
Ecodesign opportunities for promoting circular plastics in WEEE:
• Utilising recycled feedstocks for non-essential components, and easily recyclable plastic feedstocks.
• Improving product design so that components and materials are easily separated and sorted to support recycling and reuse, including the use of mono-materials for better recyclability.
• Supporting the development of collaborations between producers, PROs, recyclers, and converters (even on the product category level).
• Connecting material sustainability considerations, especially recycled plastic, to the eco-design directive.
• Extending the product lifetime and repairability, upgradeability, and modular reusability of products.
• Improving the separation and recycling systems.
• Developing tools, resources and guidance for companies and designers.
• Communicate material sustainability to consumers through (eco-)labels.
-
Example 1: Electrolux Vacuum Cleaner - Design from plastic recycling and reuse
A vacuum cleaner developed by Electrolux and Stena Recycling is made from recycled plastics recovered from small household appliance waste treatment and also reused components.
-
Example 2: Philips Senseo - Design from plastic recycling for food contact application
Philips has created a coffee machine called Senseo, which consists of 50% recycled plastics. This is a high share of recycled plastics in a food contact application.
-
Example 3: ACER Vero Laptop - Design from plastic recycling, durability and repairability
Design from plastic recycling, durability and repairability: Computer manufacturer ACER has designed and developed the Aspire Vero Laptop, which is made from PCR plastics and designed for durability and repairability. Repairability is enhanced for example by using standardized screws.
End-of-Life Vehicles is a more consistent waste stream than e-waste, in that there are common components made from specific types of plastic which could be targeted for moving towards more circular plastics in vehicles. This could be through improving the design of the vehicles, as well as the systems and services that surround them.
After removing reusable and valuable components, the remaining waste is commonly treated together with large WEEE, and fractions from the industry and construction and demolition activities.
In the EU, extended producer responsibility (EPR) is mandatory within the ELV Directive, which puts the responsibility for the collection, recycling and end-of-life disposal on the producers, but this is however managed often by national companies.
Ecodesign for ELV
Ecodesign opportunities for promoting circular plastics in ELV:
• Stricter policies on take-back and material specific or stricter recycling targets.
• Opportunities in promoting PRO schemes: Improve take back, separation and recycling systems.
• Opportunities for closed-loop systems with specific components (e.g., bumpers, tanks, covers).
• Utilize easily recyclable plastic feedstocks and modular design to support recycling and reuse.
• Increase access to information on composition of plastics in car industry.
-
Example 1: Plastic car bumpers - Design from plastic recycling with improved collection
The Plastics Industry Association (PLASTICS) and plastics recycler Ultra-Poly Corp. have successfully tested a process to collect and recycle car bumper covers made of plastic. Used covers are collected directly from body shops, where the bumpers are removed from automobiles and their reusable connected components salvaged.
-
Example 2: Fuel tanks - Design from plastic recycling and reuse with advanced recycling
Approximately 5.3 % of the ELV plastics are dismantled PE fuel tanks. Heavily contaminated fuel tanks that are traditionally sent to incineration, could prove an additional plastic source for recycling via technologies where the BFRs are removed using, for example, solvent based physical recycling such as Creasolv® and pyrolysis. The fuel tanks are commonly monomaterial PE and are thus easily recyclable after removing the contaminants.
Construction waste is a heterogeneous mix of various materials, with minerals as the main component and very little plastics. The construction industry has, in most cases, a considerably longer use phase than both WEEE and ELV, which means that the materials found in the demolition stage can vary considerably and sometimes can be difficult to identify for recycling. However, there is lots that could be done to improve the way that buildings are constructed to enable greater recycling of plastics at all stages of building.
A large quantity of CDW consists also of leftovers and waste from current construction processes including also a lot of packaging waste. As a result, the easiest potential is in improving plastic waste collection at construction sites. Systems of more controlled waste management, demolition practices, and improved management of data on contents of building materials are needed to develop end-of-life management of plastic in the building sector.
Ecodesign for CDW
Ecodesign opportunities for promoting circular plastics in CDW:
• Utilizing recycled and easily recyclable plastic feedstocks in construction products and packaging.
• Improving take back, separation, and recycling systems in the construction sector.
• Developing sorting and collection at the end of use-phase; Improving take-back, selective demolition, site sorting and separate collection.
• Improving waste management processes, for example with building information modeling (BIM) data, material tracing, certificates.
• Closed-loop systems and take-back schemes for specific materials (e.g. PVC pipes).
• Promotion of the use of recycled and easily recyclable plastic feedstocks in construction products and packaging.
• Increasing access to information on composition of plastics in the construction industry.
-
Example 1: PVC plastics - Design improved collection and management of feedstock
In the CDW sector in Germany, there is a separate collection system for PVC plastics such as pipes and tiling which enables closed-loop system around specific products.
-
Example 2: Certified Demolition - Design improved collection and management of feedstock
‘Certified demolition’ as a concept calls for more controlled data gathering on materials in demolition projects, and more specific material recycling targets for certain materials.
Summary of NONTOX ecodesign
The overall ecodesign considerations for plastics, especially focused on their use and recycling from WEEE, ELV, and CDW, can be distilled into four general eco-design recommendations for the NONTOX project context:
Design for recycling: Use recyclable materials that are easily separated and comply with recycling systems; Consider also the safety aspects of chemical additives
Design for dematerialization: Design with less materials and processes, or with ones with less impact; Promote use of recycled materials
Design for reuse and refurbishment: Support repairability and modular design; Remember user safety issues also
Design for end-of-life: Use modular design and easily detachable material components; Don’t design products but product-systems with take back mechanisms